Rail mounted container gantry cranes (RMG cranes) are indispensable pieces of equipment for efficient container handling operations at ports. These cranes are designed to load, unload, stack, and transport containers within port terminals, ensuring smooth and timely operations. Using an RMG crane correctly requires an understanding of its features, capabilities, and safety measures. In this guide, we will discuss how to effectively use a rail mounted container gantry crane at a port and ensure smooth, safe, and efficient container handling.
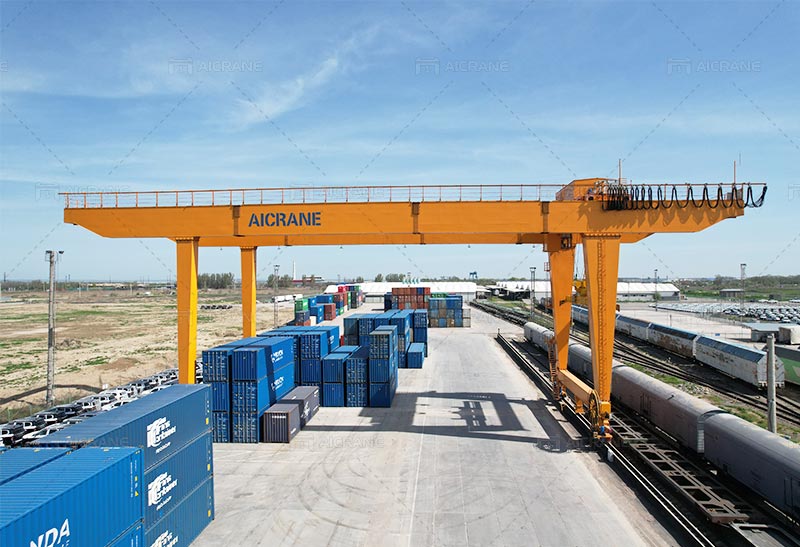
Understanding the Rail Mounted Container Gantry Crane
Before using an RMG crane, it is essential to understand its structure and functionality. These cranes run on rails and are specifically designed for yard stacking and container handling in ports and terminals. Unlike rubber-tyred gantry cranes (RTGs), which are mobile and run on rubber wheels, rail mounted container gantry cranes operate on fixed tracks, making them highly stable and efficient for handling heavy loads in repetitive operations.
Key features of RMG cranes include:
High Lifting Capacity: RMG cranes can handle containers of various sizes, such as 20-foot, 40-foot, and even 45-foot containers.
Long Spans and Tall Heights: These container gantry cranes are capable of spanning multiple container rows, making them ideal for high-density stacking.
Precision Handling: The rail-mounted design ensures accurate movements, making it easier to place containers precisely on stacks or vehicles.
Preparing for Operation
Before operating a rail mounted container gantry crane, operators must ensure that both the crane and the port area are ready for safe and efficient operations. This involves several steps:
Inspection: Conduct a thorough inspection of the crane and rails before starting any operations. Check the hoisting mechanisms, spreader, ropes, tracks, and electrical systems to ensure they are in good working condition. Look for any signs of wear, corrosion, or potential hazards.
Track Clearance: Make sure the tracks on which the crane moves are clear of obstacles. Since the crane is rail-mounted, it relies on an uninterrupted rail system for horizontal movement. Any obstructions can cause delays or accidents.
Safety Systems Check: Verify that all safety systems, including anti-collision sensors, emergency stop buttons, and load limiters, are functioning correctly. These systems are essential for preventing accidents during crane operations.
Weather Considerations: RMG cranes are sensitive to weather conditions such as strong winds, rain, and fog. Check the weather forecast before starting operations, and if conditions are unfavorable, postpone the operation to ensure safety.
Operating the Crane
Operating a rail mounted container gantry crane requires skill and precision. The crane operator must be well-trained and familiar with the controls and safety protocols. Below are the key operational steps:
Lifting and Lowering Containers: The crane uses a spreader to lift containers from ships or trucks and move them to storage areas or other locations. The operator must align the spreader precisely with the container’s corner fittings, lock it in place, and lift the container smoothly.
When lowering containers, it is essential to ensure that the container is placed correctly on the designated location without causing damage to the containers or the surrounding equipment.
Horizontal Movement Along the Rails: The crane moves horizontally on rails, which allows it to travel across the container yard to stack containers. This movement is controlled from the operator cabin or a remote control system. The operator must monitor the surroundings and avoid collisions with other equipment or structures.
Stacking Containers: Stacking containers efficiently is a crucial part of port operations. RMG cranes are designed for high stacking, allowing up to 6 to 8 containers to be stacked on top of each other. This optimizes the use of space in the container yard. The operator must ensure proper stacking alignment and follow stacking protocols to avoid instability or collapse.
Load Monitoring and Control: The crane’s load monitoring system helps the operator stay within safe lifting limits. Exceeding the crane’s capacity can cause damage or accidents. Ensure that the crane’s load is within its maximum capacity and avoid overloading.
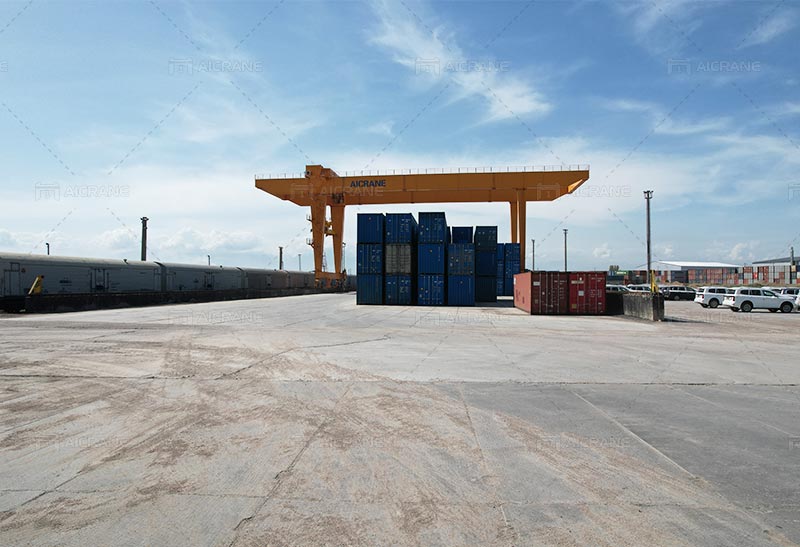
Safety Protocols
Safety is of paramount importance when using a rail mounted container gantry crane at a port (https://aicranemachine.com/solutions/logistics-port-transportation/). Operators and ground staff must adhere to strict safety protocols to prevent accidents and ensure smooth operations.
Operator Training: Only qualified and trained operators should handle RMG cranes. Proper training includes understanding crane controls, load management, safety systems, and emergency procedures.
Ground Communication: Maintaining clear communication between the crane operator and ground staff is essential for safe operations. Use hand signals, radios, or other communication systems to coordinate movements and avoid confusion.
Safe Zones: Ensure that no unauthorized personnel are in the crane’s operational zone. Ground staff must stay clear of the crane’s path and the area where containers are being lifted or lowered.
Emergency Procedures: Be familiar with the crane’s emergency stop procedures. In case of malfunction or an emergency, the operator must be able to stop the crane immediately and safely lower the container.
Maintenance of the Rail Mounted Container Gantry Crane
Regular maintenance of the RMG crane ensures its longevity and operational efficiency. Here are some maintenance tips:
Rail Maintenance: Since the crane operates on rails, keeping the tracks clean and free of debris is critical for smooth operation. Conduct regular inspections of the rails for any cracks, wear, or misalignments.
Mechanical and Electrical System Check: Regularly inspect the crane’s hoisting system, spreader, ropes, and gears for wear and tear. The electrical components, including motors and control systems, must also be checked to prevent breakdowns.
Lubrication: Keep all moving parts well-lubricated to reduce friction and prevent premature wear. Regularly apply the appropriate lubricants to the crane’s gears, cables, and tracks.
Weather Protection: If the crane operates in an environment with harsh weather conditions, take steps to protect it from rust and corrosion. This may include applying protective coatings and storing the crane in a sheltered area during long periods of inactivity.
Efficiency and Productivity Tips
Maximizing the productivity of a rail mounted container gantry crane involves optimizing both the crane’s operation and the layout of the container yard.
Optimized Yard Layout: Plan the container yard layout to minimize the distance the crane needs to travel along the rails. Group containers based on destination or size to reduce handling time.
Load Sequencing: Organize container loading and unloading in a sequence that minimizes crane movement. Efficient sequencing helps avoid unnecessary crane travel and increases the speed of operations.
Technology Integration: Many modern RMG cranes come equipped with automation and tracking systems. These systems can help optimize container handling, reduce human error, and improve overall efficiency.
In conclusion, using a rail mounted container gantry crane at a port requires a combination of skill, precision, and adherence to safety protocols. From preparing the crane for operation to maintaining it regularly, every step is crucial for ensuring smooth and efficient container handling. By following the best practices outlined in this guide, port operators can maximize the productivity of their RMG cranes while ensuring the safety of both personnel and cargo. Proper planning, regular maintenance, and operator training are the keys to successful operations with rail mounted container gantry cranes at ports.